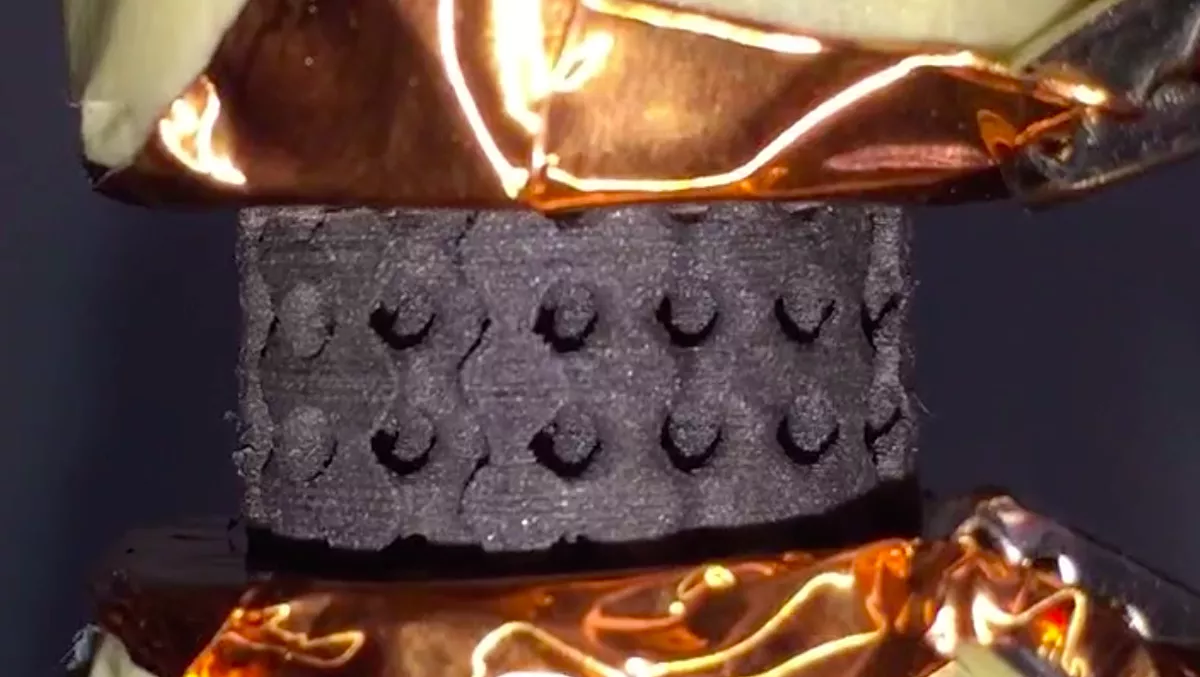
Nanotech brings tough, flexible sensor to life
Researchers have created a new sensor technology that combines nanotechnology and 3D printing to produce a durable and flexible product that could produce a new wave of wearable technologies.
Developed by engineers at Canada's University of Waterloo, the sensor is designed to be able to monitor everything from vital signs to athletic performance.
The new technology combines silicone rubber with ultra-thin layers of graphene in a material ideal for making wristbands or insoles in running shoes
When that rubber material bends or moves, electrical signals are created by the highly conductive, nanoscale graphene embedded within its engineered honeycomb structure.
Mechanical and mechatronics engineering professor Ehsan Toyserkani says that the rubber-graphene sensor can be paired with electronic components to make wearable devices that record heart and breathing rates, register the forces exerted when athletes run, allow doctors to remotely monitor patients and numerous other potential applications.
"Silicone gives us the flexibility and durability required for biomonitoring applications, and the added, embedded graphene makes it an effective sensor. It's all together in a single part." says Toyserkani, who is also the Waterloo Multi-Scale Additive Manufacturing (MSAM) Lab research director.
It took using the latest state-of-the-art 3D printing equipment and processes to fabricate a silicone rubber structure with such complex internal features.
The rubber-graphene material is extremely flexible and durable in addition to highly conductive.
"It can be used in the harshest environments, in extreme temperatures and humidity. It could even withstand being washed with your laundry." says the project lead, engineering PhD student Elham Davoodi.
The material and the 3D printing process enable custom-made devices to precisely fit the body shapes of users, while also improving comfort compared to existing wearable devices and reducing manufacturing costs due to simplicity.
Researchers from the University of California, Los Angeles and the University of British Columbia collaborated on the project.
More information on the project, as well as videos demonstrating the material's resilience, are available in the latest in a series of papers on the research, 3D-Printed Ultra-Robust Surface-Doped Porous Silicone Sensors for Wearable Biomonitoring, appears in the journal ACS Nano.
While smartwatches are currently dominating the wearable tech segment, daily usage rates of fitness trackers (at least in mature economies) are on the rise and many fitness tracker companies are exploring growth opportunities in healthcare services, according to GlobalData.
The ability to incorporate sensors into malleable and resilient materials may be one step toward the greater proliferation of wearable fitness trackers for professionals and consumers.